Working in warehouses can be very demanding. High physical exertion, 3-shift work, and the risk of injury are just some of the drawbacks that employees complain about. One of our clients approached us with an idea to streamline warehouse processes and ease the burden on their team. Engaging a robot and artificial intelligence to do the work turned out to be exactly what they needed.
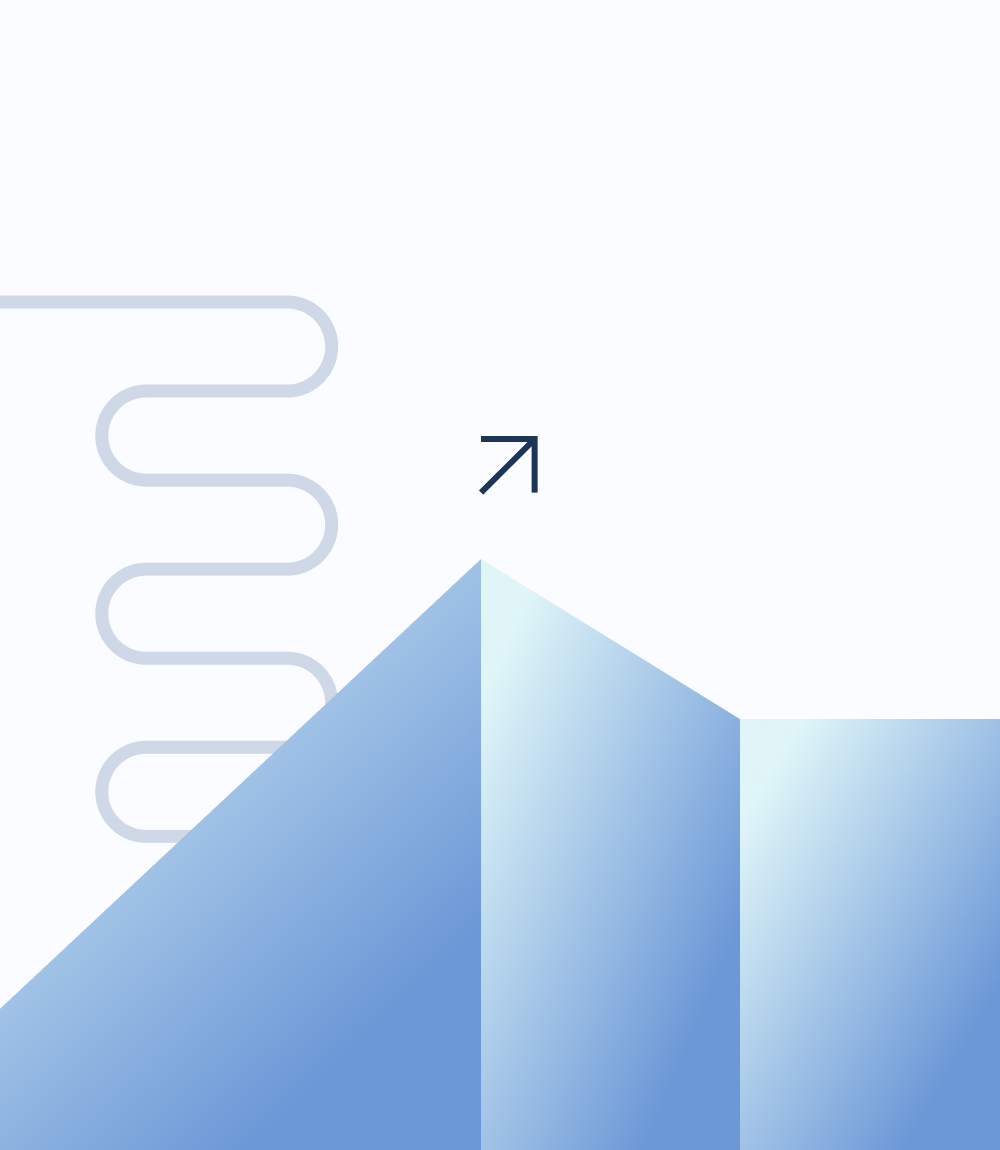
Employee comfort and health issues are just some challenges facing companies responsible for handling warehouses. They are bustling places, so there is often no time for comprehensive training and a lack of people to teach novice warehouse workers. This leads to their frustration and can contribute to their mistakes. These, in turn, can disrupt the smooth operation of the warehouse. It should also not be forgotten that warehouses are often located in the suburbs. That's an additional cost (borne by the employees themselves or their employers) and additional commuting time.
There are also challenges on the economic side of running such a business. The hard work of human hands is associated with increasing financial burdens, which in times of rising prices and inflation can significantly deplete earned income. And this is where the world of revolutionary new technologies comes in, which can help optimize costs, speed up work, and create even more efficient processes for warehouse operations.
Why trust robots in warehouses?
At Primotly, we love challenging projects, especially those where innovation can really help people. After we analyzed all the information provided to us by the client, we visited his warehouse to carefully prepare for planning our work. However, one thing was certain from the very beginning – we knew that our artificial intelligence algorithms, machine learning, and robots would be invaluable support with great potential here.
Human brain VS. machine learning
Although there is not always time for comprehensive training for employees in warehouses, the human brain learns very fast. Employers master their duties fairly quickly, but repetitive tasks quickly begin to bore them. Routine comes to the fore, often involving a lack of accuracy. This problem does not apply to machines. Artificial intelligence needs more time to learn certain activities from scratch. However, tasks are completed faster and more accurately once the entire process is perfected. And above all, there is no place for human mistakes anymore.
Quick return on investment
Before we get into the specific improvements we have planned for our client's warehouse, it is worth mentioning what matters most to the business – cost optimization and savings. Each employee is a fixed cost for the company that recurs annually and often increases over time. In the case of machines, we are dealing with an investment that quickly pays for itself after a set period of time. In this way, the employer saves money spent on the salaries of live workers (yes, robots don't have unions to change that yet 😄). At the same time, the efficiency of the machines increases the productivity of the warehouse and this also helps increase profits.
Solving the problems of the warehouse
Okay, it's time to get specific. The client we work with runs a business, of which product returns are an integral part. Returned items are reused in subsequent orders. Each year, it takes a lot of time and tons of money to get them to the warehouse, unpack, describe, count, and prepare for reuse. It's a very green solution, but one that also requires additional logistics and costs. And after all, doing good deeds for our planet should be rewarded! Of course, additional costs are included in the product, but you also have to pay the employees who handle this process in the warehouse. And that's where the idea of relieving people of this tedious work with robots came in. A machine that already knows how to perform a certain task can work 24 hours a day. It would take 3 people working 3 different shifts to do its job. And at the same time, robots do the job accurately and even faster than humans.
Robots handling returns in the warehouse
After analyzing the existing system of receiving returns to the warehouse, we have identified key tasks in which human labor will be replaced by robots supported by AI algorithms:
scanning the barcode,
opening the carton box with the products,
counting products,
removing the products from the carton box,
save the information in the database.
We carefully planned the scope of work for each stage of the process. Each successive step saves human resources. The first robot will be lining up carton boxes from a pallet onto a conveyor belt. These will be scanned and counted. Another robot will unpack them. All information will be transferred to the database. According to preliminary calculations, about 10 seconds will be saved on each cardboard box, which would have to be spent by a human!
There is no need to reinvent the wheel
In order to optimize costs, we decided to use many off-the-shelf technological solutions (both in terms of hardware and software). In our work, we always proceed from the assumption that there is no need to reinvent the wheel. If a solution is already available on the market and works very well, it is a waste of time to write new programs or construct devices from scratch. The project is still in the development and implementation stage, but below you will find a detailed description of the activities we have already finished and planned for the coming months.
AI in the warehouse: the process
It's time to review the solutions we decided to implement. Let's start with the first step, which has already been tested and refined.
Automatic Barcode Scanning
When boxes of returns arrive at the warehouse, they must first be indexed in the system. As for hardware, at this stage, it was enough to use any good-quality camera, without having to reach for more advanced equipment. We wrote a suitable program in Python. The code could later be adapted to ready-made barcode readers - Cognex or Sick. It is worth knowing that already at this stage of prototype work we have visited the target warehouse where our system will be implemented. This allows us to test our solutions right away in real environment.
Mechanical Edward Scissorhands
Another robot we are currently working on will open cardboard boxes after the bar codes have already been scanned. In this case, we used excellent hardware from CASi. Their IBOD (Intelligent Box Opening Device) is an inline, pass-through box-opening solution with an automated box-cutting function. Boxes can be arranged in any order by any size. CASi-IBOD measures their size to ensure precise cuts for each box. This allows products to be removed quickly later, eliminating the need for a warehouse worker to use scissors or knives. CASi-IBOD is a fully automatic system. It uses photo-optical measurements and linear displacement to size each box. Once a box is sized, it is automatically captured and positioned for cutting.
Automatic Counting of Products Entering the Warehouse
After opening the boxes, it is necessary to count the products coming into the warehouse. We are assisted in this task by the Luxonis Oak-D-Lite camera. The device collects images of items. Based on them, special labels are prepared to recognize specific objects. We also used TensorFlow models. Thanks to AI, the code we created in Python allows us to compare products and recognize them according to the data in the prepared repository. Currently, we are spending most of our time on the development of the Luxonis camera work. Once this stage of the process is completed it will be time for the final step…
Warehouse Robot Never Gets Tired
The task for the last robot is to remove the returned products from the carton boxes. At this stage, we plan to use intelligent technology for item handling developed by Mecalux.
Robot arms with grippers designed to lift products will automatically pull the items out from pre-cut cartons. A refined pick & place process ensures proper operation efficiency and allows even better optimization of the time needed to handle returns in the warehouse. The work is moving forward day by day, and we can't wait to start the tests, which will include all stages of automation. When everything is ready we will definitely let you know on our blog.
If you have questions about innovative solutions for your business, are looking for new ways to optimize costs in your warehouse, or want to work together on a similar project, let us know. We'd love to meet you and talk about how we can help.